Turning fictional technology into a reality
The recent boom in the development of smart textiles and smart clothing is producing a range of textiles incorporating sensors and flexible wiring using special conductive fibers, dyes and other materials. These textiles are made into clothes capable of sending and receiving detailed physical data on the wearer, such as their pulse and ECG readings and minute movements. These novel fabrics are creating new utility value that conventional clothing lacks; for instance, in addition to their application in virtual reality (VR) games, such smart clothing can be used to remotely check the physical condition of workers, people receiving care or anyone else as required. Japanese textile manufacturers are well represented in the development of materials supporting these new technologies.
So what exactly are smart textiles and smart clothing? Smart textiles are equipped with sensors and other information communication technology (ICT), while smart clothing refers to the wearable ICT devices made from smart textiles.
Another common question is why is there now such a boom in the development of smart textiles and smart clothing? The answer can be traced to the remarkable advances in ICT, which are producing increasingly sophisticated smart wearables that can be commercialized for consumer use.
It’s not that we’ve never seen such smart wearables before. They appear often in the fictional world of movies and animation, such as sunglasses that can assess your opponent’s fighting abilities and sneakers that automatically fit to the shape of your feet. So the ideas themselves have always been around. It’s just that now we have the ICT to make these futuristic devices a reality, and this is what is driving the current development boom.
Backed by advances in ICT
Recent advances in ICT can be roughly summarized in the following three points.
1 High speed processing of large capacity data using less power.
2 Increasingly sophisticated sensing technology, which is producing thinner sensors that are as small as the size of a person’s little finger nail. These sensors meet the minimal requirements for use in smart wearables, namely maintaining performance even when bent or stretched and being wash durable.
Points 1 and 2 are key elements in making smart textiles much more comfortable for the wearer.
3 The push to develop data analysis software, and also application software for the analyzed data. This software supports the creation of data-based services to meet the varied needs of users.
Although the current market for smart wearables (watches and bracelets/wristbands, glasses, head-mounted displays, clothing, etc.) is relatively small, according to some market research companies, the majority view is this market is set to rapidly expand going forward. One such company, Yano Research Institute Ltd., estimates the global market for smart wearables will reach 322.8 million units by 2020, which is 2.8 times the 2016 size, with the Japanese market expected to triple in scale to 11.6 million units.
In contrast, the US market research company IDC forecasts the 2019 global market for smart wearables will be 1.7 times larger than the 2015 levels on a monetary base, and 2.9 times greater in terms of units sold. The price variation among smart wearables is cited as one of the reasons for sales in dollar terms not keeping up with units sold.
Looking at the market by individual items, Yano Research Institute data estimates around 90% of smart wearables sold in Japan and worldwide are watches and bracelets/wristbands. These include the numerous examples we can already see on the market, such as devices that measure daily activities and smart watches from Apple and high-end fashion brands.
We can expect to see a wider range of smart wearables, including smart clothing, to gradually hit the market from hereon. IDC also forecasts the share of watches and bracelets/wristbands to drop to 80% of smart wearables sold compared to 90% in 2015, with smart clothing accounting for 5% of this.
Adding value to conventional clothing
The Internet of Things (IoT) and the emergence of smart wearables are closely linked.
Everyday items are becoming increasingly connected to the internet, and the combined strengths of sensors and software are starting to produce even better utility value. Every existing item can produce better value through the innovation of the so-called IoT (Internet of Things). The development of smart wearables is a part of the IoT wave, and it includes smart clothing – perhaps the most wearable item for people.
The current proposed usages of smart clothing are in sports and health and nursing care. Smart clothing uses sensors to detect and measure specific physical data such as pulse and ECG readings, as well as joint and muscle movements. This data is then used as required to create utility value.
For instance, smart clothing can detect the signs of a seizure and alert the wearer’s doctor, or it can help athletes train more effectively and know when to rest as required. There is also a move toward launching services combining artificial intelligence (AI) with the analysis and application of smart data. So we can expect to see even more high-value services linked to smart wearables.
Japan’s strength is in materials development
Japan’s development of smart wearables is led by its material manufacturers and their enthusiastic embrace of smart textiles.
The forte of Japanese textile manufacturers is their high-function fibers and associated processing technology, of which the first widely known example is hitoe™, jointly developed by Toray Industries Inc. and the Nippon Telegraph and Telephone Corporation (NTT) in January 2014. hitoe™ uses sensing technology to detect faint electrical signals emitted by the heart, muscles and other areas of the body, including brain waves.
hitoe™ is a highly-conductive nanofiber textile consisting of nanofiber knit infused with conductive polymers. Infusing textiles made of normal polyester fibers with conductive polymers leaves large gaps between the fibers, which causes the conductive polymers to easily detach and fall off when the fabric is washed.
However with a nanofiber such as hitoe™, the conductive polymers enter and fix themselves in position within the small gaps between the nanofibers; so the garment can be worn over a long time and washed repeatedly without losing functionality.
The sports apparel maker Goldwin Inc., which runs The North Face and other sports brands in Japan, was one of the first in its industry to launch smart inner wear at the end of 2014. Anticipating heat stroke and similar conditions that affect construction site workers toiling under the scorching sun, last summer the company launched a “Watch-Over-Worker Service” and other initiatives for looking after the health and safety of people working outdoors.
Leaders in conductive fibers
One Japanese manufacturer of conductive fiber that has been particularly active of late is Mitsufuji Corporation. The company’s AGposs® conductive fiber is the product of its well-developed original technology, which has created a fiber metalized with silver on the surface of nylon or polyester, giving it excellent conductivity. Mitsufuji has been busy expanding its business beyond Japan, as it works on developing smart wearables primarily for use in medicine and health care both domestically and overseas.
Mitsufuji was founded as a Nishijin textile factory, and since the 1980s the company has been drawing on its ancestral technology to develop wearable conductive fibers.
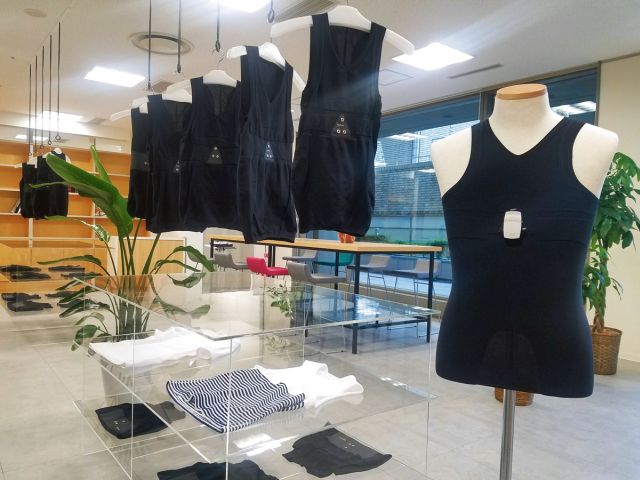
Mitsufuji’s display at the wearable showroom in Tokyo in July. The company is accelerating open innovation.
Last December Mitsufuji launched its own smart wearables brand hamon®, of which the first product range was seamless and comfortable underwear made from soft and stretchable knit fabric. The company uses the WHOLEGARMNET flat knitting machine to create seamless garments which, unlike conventional clothes, have no notable seams around the shoulders, hems, cuffs and collars. hamon® products are practical with a focus on comfort as clothing, combined with functionality as smart wearables.
Mitsufuji is presently inundated with inquiries from sports companies, care services and other areas both in Japan and overseas, to a level that is stretching its current production capacity. So the company is now scrambling to set up a system for mass production, including opening an AGposs® factory in Kyoto’s Nantan city in April 2018 that will double its present production capacity. Later that same year, it will also open a factory for the integrated production of smart wearables in the town of Kawamata in Fukushima prefecture. MITSUFUJI is currently developing the next generation AGposs®2.0 with even better conductivity, which it plans to make an official release in January 2018. The new and improved AGposs ® will have an even coating of double the silver used in the current version, and the added property of elasticity.
hamon® is more than just a smart wearable; it combines a miniature device that transmits sensing data with a cloud service that analyzes the data. It uses a completely self-developed and integrated system for all processes, from developing and producing the fibers to offering cloud services. Mitsufuji is a world pioneer in that sense, and accordingly the company has set its sights on becoming a global standard for IoT smart wearables originating in Japan.
Commercialization on the horizon
Mitsufuji has trail blazed the way for other companies to pick up the pace in developing smart clothing these past few years, and the outputs are steadily approaching the commercialization level. Despite previous problems of notable noise and accuracy issues with measured data, the items seen at recent exhibitions are actually complete enough to be being worn by the attendees there, who can also have their physical data measured. As one manufacturer pointed out, “We are starting to see an outline of how we can turn smart clothing into a viable business.”
As mentioned above, smart clothing is also seen as a promising solution to various issues in the fields of medicine and sports, including being used to detect the signs of a seizure or for more effective sports training and knowing the right time to rest. Transport companies and operators of long-distance buses have also cited the need for smart clothing. These companies want their drivers to wear smart clothing so that they can monitor their physical condition, and avoid accidents by detecting when the driver is feeling ill or asleep at the wheel.
The smart apparel start-up Xenoma Inc.—a spin off from the University of Tokyo — is also floating the idea of using smart clothing to manage factory floor workers and help them learn on the job more effectively.
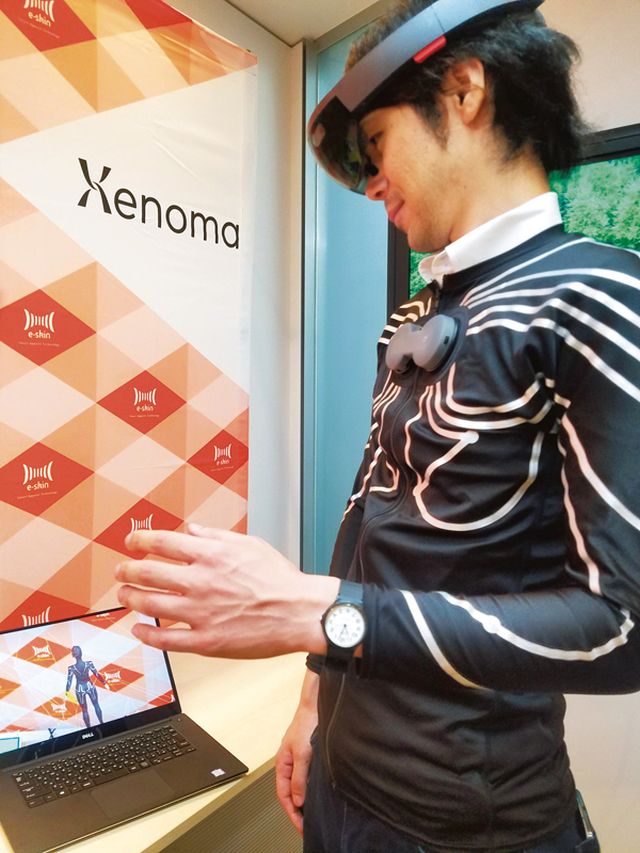
Mass-producer of smart wearables Xenoma. VR service provided in collaboration with Microsoft’s HoloLens.
This spin-off company was launched in November 2015 with the aim of commercializing e-skin, a highly elastic fabric featuring printed electrical circuits made of conductive ink. Xenoma’s smart clothing made of e-skin is equipped with 14 strain sensors that can even sense the wearer’s minute body movements as electrical signals. A compact device attached to the clothing collects these signals, and then sends them via Bluetooth to a smart phone, PC or other device.
Recently the company has added a purpose-specific motion assessment function to e-skin that uses Google’s AI platform TensorFlow.
This new function can be used to assess whether factory floor employees are working properly or dangerously by comparing their actual movements to model examples, and then determining the variance rate between both. e-skin also has potential uses in industrial safety and training, and in improving form and performance in any sport.