From JFW-JC2017, PTJ Autumn/Winter 2018-19
The JFW Textile Fair is Japan’s leading textile event. The JFW JAPAN CREATION, a general textile fair, and Premium Textile Japan (PTJ), a textile business negotiation salon are set to be held jointly, bringing together around 400 businesses, mainly domestic textile companies. Last year the same event was held on the 28th and 29th of November, and a standout number of visitors from the overseas clothing industry attended the event. We saw buyers from Europe, America and the Middle East, as well as Japan’s near neighbours, such as China, Korea and Taiwan. What is it about Japanese materials that attracts overseas clothing professionals? Below are some of the recommendations from the exhibitors themselves.
A fusion of advanced technology and craftsmanship
Much attention has been paid to Toray Industries, Inc.’s new down jacket, created with a novel textile the company released last year, ‘uts-FIT’. Using proprietary spinning technology, the company has managed to fully maintain the smooth and supple texture of superfine polyester, combining it with a fullness and stretch not normally achievable with superfine fibres.
While soft, the textile has a unique feel and is quite strong. It also has a shine to it that gives it a high-class feel. Even if crumpled into a ball, any creases on this textile will soon fall out while worn.
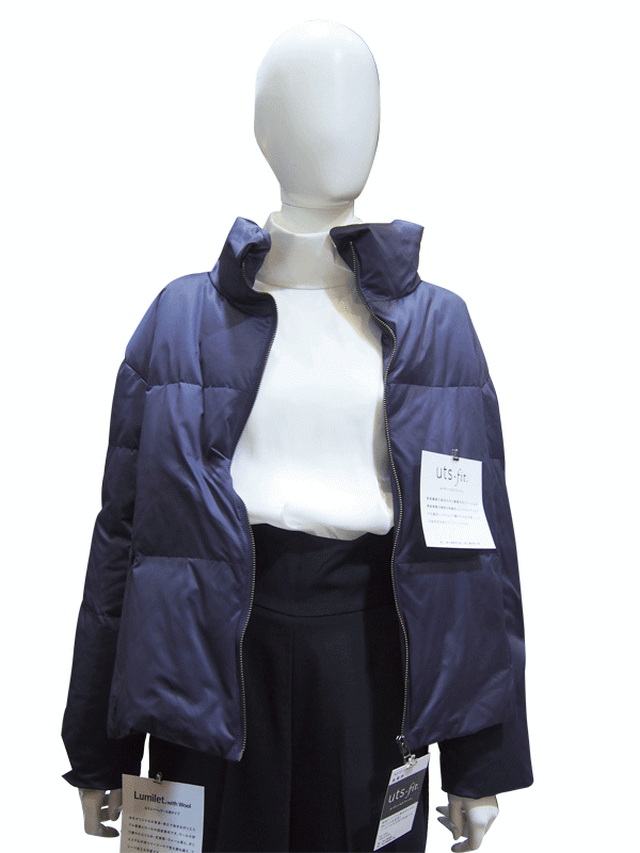
Toray
Daiichi Orimono Co., Ltd., a maker of high-density synthetic fibre fabrics, has been developing a “fashionable synthetic fibre for creating new down outerwear”. It is normal for down to have a crisp texture, but softness is emphasised in Daiichi Orimono’s nylon ‘D.N.A. Light’ and its cotton-like polyester ‘mauri’. Unquilted down jackets have a fluffy and rounded form, and it is possible to give them gathered designs.
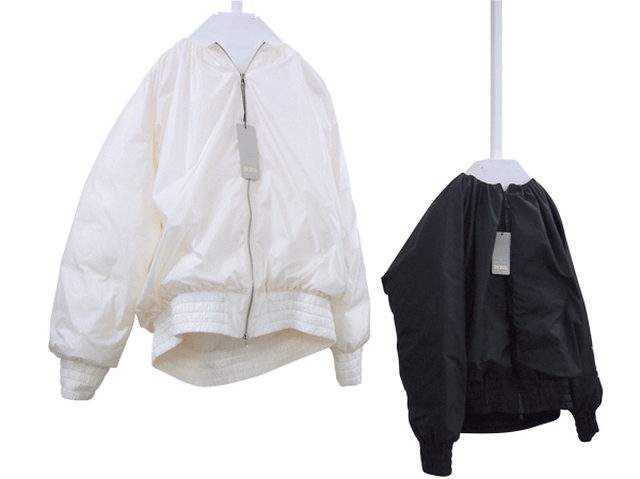
Daiichi Orimono
Using synthetic fibres, the Marui Group has proposed a vast line-up of comfortable materials for everyday wearing. Marui has come up with various cloths with bright botanical prints, inspired by Hawaiian shirts. Made with synthetic fibres, they are highly practical, being washable and relatively crease-resistant.
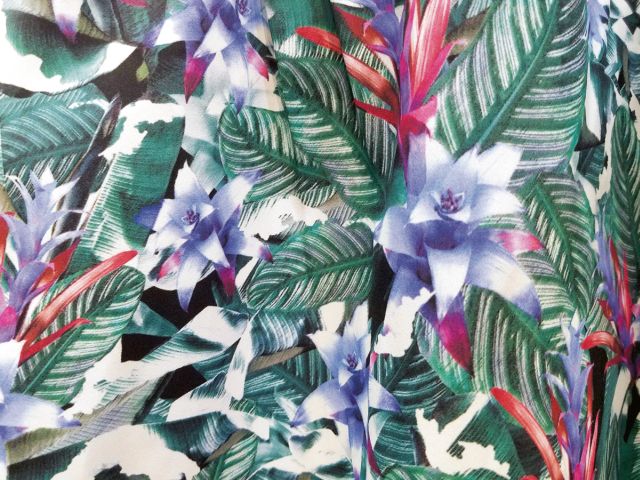
Marui Group
Ochiai Lace Co., Ltd., a trading company specialising in lace, is known for incorporating advanced Japanese lace-manufacturing technologies in creations that capture the mood of the market, and many of its products have been picked up by luxury brands.
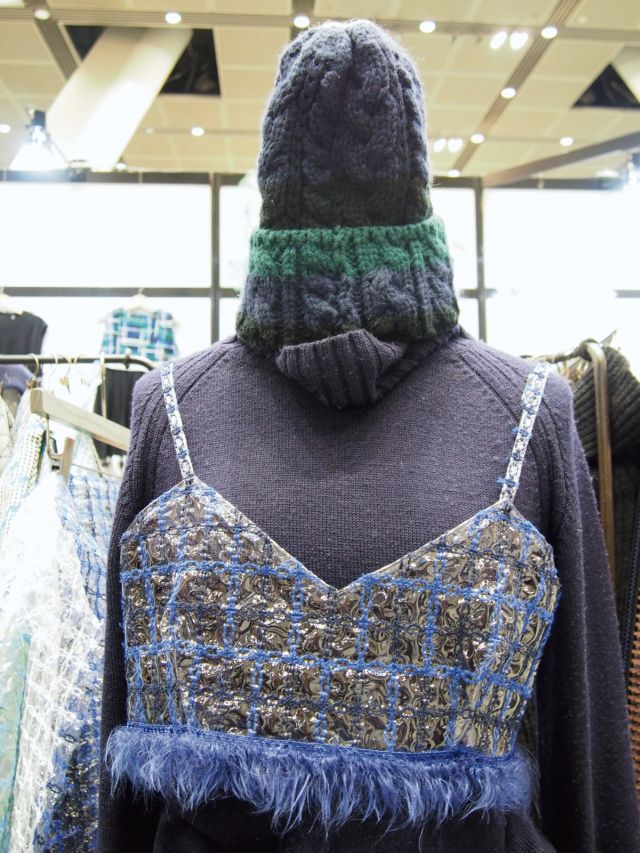
Ochiai Lace
Our recommendation is the company’s sheer lace made with techno material. Created with fishing gut, the lace is supple, and the detailed patterns are expressed delicately. The lace features PVC, a growing trend in the industry, which is used to embroider the check pattern with fluffy mohair thread, giving rise to fringe-like piles and emphasising the sheerness of the lace.
Unique natural fibres, with a focus on thread-use and finishing processes
Furuhashi Weaving Co., Ltd., a weaver in Hamamatsu City, which is well-known for its cotton textile industry, is increasing production of fabrics with varied surfaces, using natural fibres. One such fabric is made using core yarn (with a wool core and cotton outside) weft, giving its surface fine bumps. The company also offers a cloth woven with washable combed wool on the shuttle, which is the perfect material for light jackets for the early autumn.
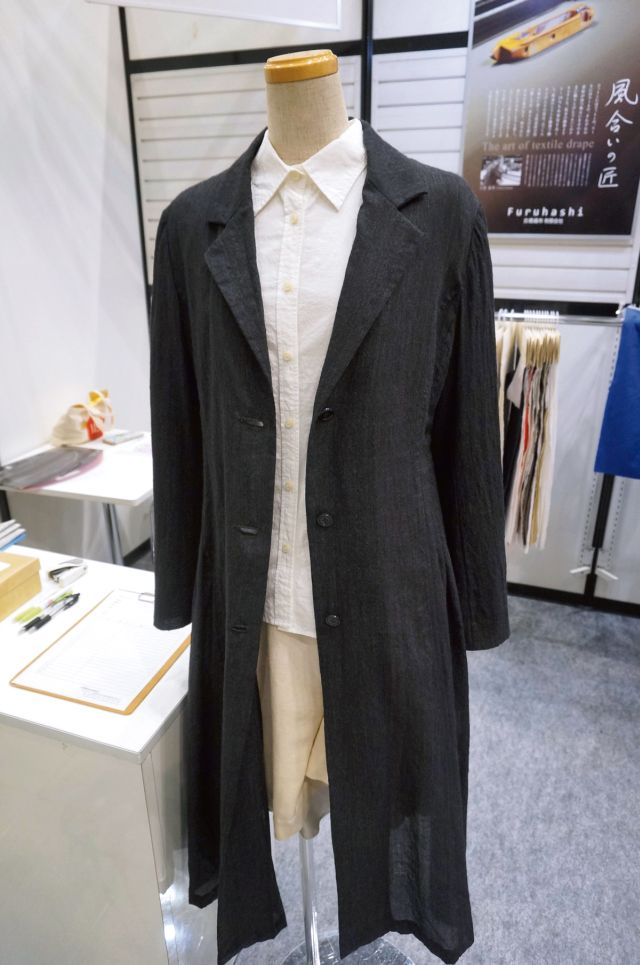
Furuhashi Weaving
Komatsuwa Textile Co., Ltd., a company that converts clothing fabric, introduces ‘azuma-daki dyeing’, a plan to develop dyeing factories. It is pushing its “relax fabric”, which maximises the full and soft texture of natural fibres, as a comfortable material for womenswear.
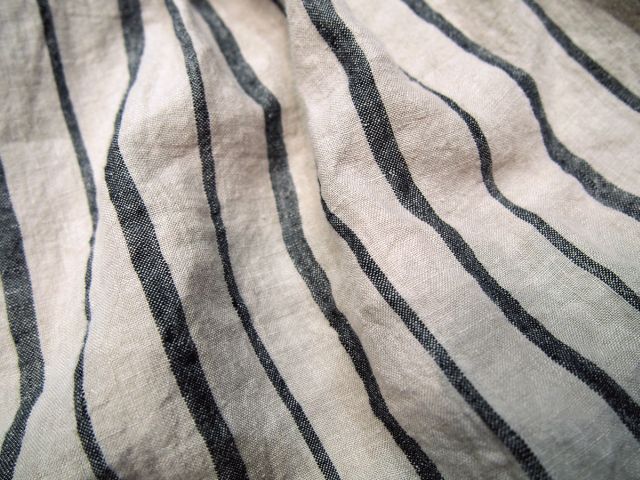
Komatsuwa Textile
‘Kama ire’ is a dyeing technique used in the Edo Period (1603-1868), where cloth was placed in a traditional Japanese bath, known as a ‘goemon buro’, mixed with lime and plant lye, and boiled. The dyeing craftsman would pay close attention throughout, adjusting the temperature and humidity and dying the cloth a small section at a time. To finish, the cloth would be dried naturally, without any direct heat source being applied. The cloth would be creased, with a relaxed finish.
Suzuki Bleach & Dyeing Co., Ltd processes natural fibres to add various features and unique appearances. The company is also considering using its newly-developed anti-crease process to expand sales into America and Europe, markets with stringent demands when it comes to natural fibres. The process reduces creases after washing in household washing machines and allows the creases to fall out easily when worn, so products made using this process have even higher potential for wash-and-wear than products that undergo regular processing.
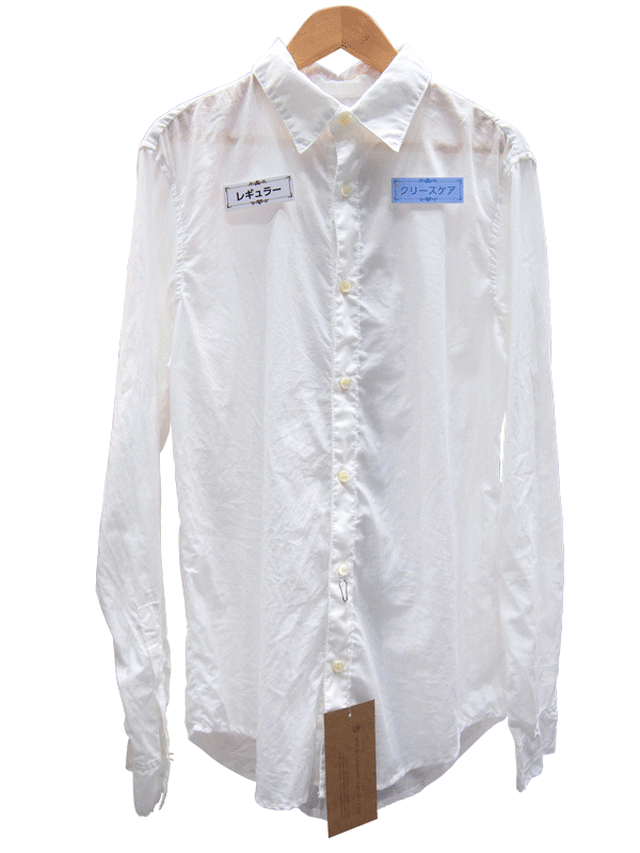
Suzuki Bleach & Dyeing
According to a proprietary formula, the company adds various chemicals to untreated fabric that raise crease resistance, even for cloths that crease easily, such as cotton typewriter cloth and cellulose ‘TENCEL’ lawn.
Denim is the mainstay of Japan Blue Co., Ltd. The company’s SHIN-DENIM, developed this autumn from cotton and polyester, has a heightened colour fastness thanks to a unique dyeing technology. Japan Blue is able to maintain the texture of the cloth, while increasing the wear-resistance to 2.5 times that of 100% cotton denim. The company is proposing a wide range of uses for the material, such as interiors or car seats.
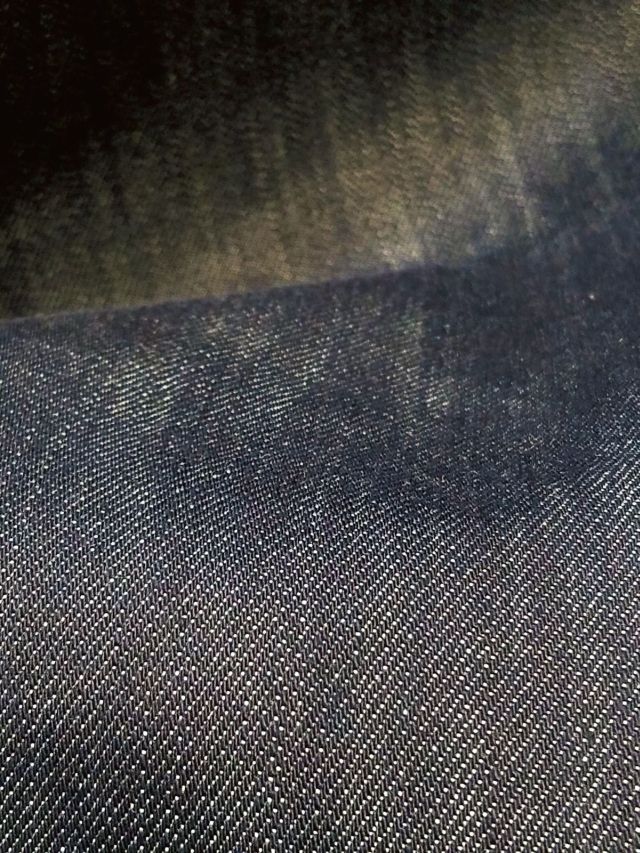
Japan Blue
Ambitiously seeking new materials through technological and conceptual innovation
Watanabe Pile Textile Co., Ltd. is a company that produces woven pile – normally used for towels – as clothing fabric. It has created a new fabric with plain weaves using a towel loom. The creation of this textile was triggered by customers’ interest in the hem at the edge of towels. The fabric surface is flat, but its appearance is enriched with mélange thread.
Wadanobutex, a torchon lace maker, has created piping made with torchon lace. A thick thread is used in the centre of a 3cm piece of lace, which is half the normal width, and the lace is made so it can be folded in half. This unique manufacturing method allows the creation of arcs, and means clothes can be finished by sewing lace inside the collar.
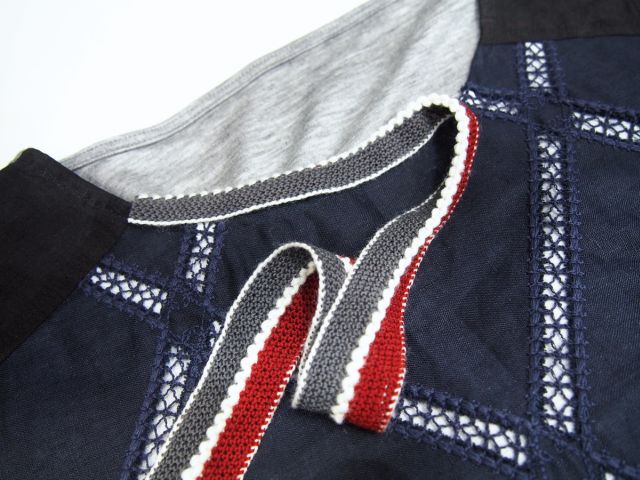
Wadanobutex
Duck Textile Co., Ltd., a trading company specialising in denim, leverages various processes to create a wide range of denim products with diverse designs. The company’s latest creation incorporates tiers made from two types of 100% cotton denim. It is largely made by hand, but the cloth cutting and sewing processes have been automated, increasing production efficiency and enabling mass production.
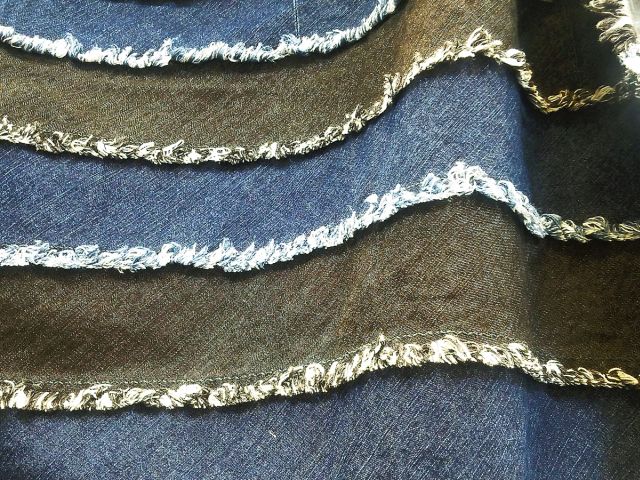
Duck textile